So you’re wondering, “How do I became a welder?” That’s a simple question with a complex answer.
Welders are skilled tradespeople who use intense heat to join metal together or repair metal structures or components. To do that, they use one of many different welding methods, the most common being arc welding, where welders use a special welding rod or wire and join two metal pieces with an arc of electrical current. Then there’s oxy-fuel welding, which uses a flammable gas and oxygen to produce the heat needed to melt and join the metal pieces together. Hold on. There’s more. Resistance welding, shielded metal arc welding, submerged arc welding, and the more modern laser beam welding processes. Most welders use hand-held equipment, but some use remotely controlled devices.
Yikes. Sorry you asked?
Don’t despair. By reading this post, you’ll go a long way toward understanding what it takes to become a welder. We’ll look at exactly what a welder does, how much he/she earns and what training is necessary to become a welder.
Ready? Let’s go.
What do welders do?
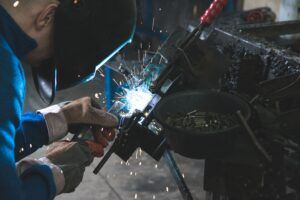
As said earlier, welders work on the metal components of various structures such pipelines, bridges, power plants, buildings, refineries, automobiles, or ships, joining metal together to make a product.
Welders primarily work outdoors in the elements—or, sometimes, under water, if they have the right training and gear.
Exactly what a welder will do on a regular basis depends on the industry they are working in—or what level of experience they have.
Typically, a welder’s day will start with reviewing blueprints and other instructions to determine what welding methods or sequences are required for the job. A welder then may lay out the metal parts and align them properly for assembly. From there, one or more of the following activities could make up the welder’s day:
- Joining metal parts in flat, vertical, or overhead positions
- Calculating dimensions of metal parts to be welded
- Laying out, positioning, aligning, and securing metal parts
- Inspecting workpieces for defects and checking for specifications
- Igniting welding torches and striking arcs
- Selecting welding methods and required equipment
- Cleaning welded metal off excess weld, slag, or spatter
- Filling holes or hammering out bulges and bends
- Maintaining equipment and machinery
How much do welders earn?
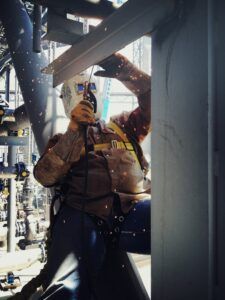
The Bureau of Labor Statistics reports that the median salary for a welder is $44,000 across the country. But that figure’s deceptive, says Jason Becker, a welder from Kissimmee, Fla., who hosts The Arc Junkies podcast.
“Obviously the type of work you get into will have a lot to do with the salary,” he said. “Field welders and those who travel will make significantly more whereas a shop welder or someone with base level skills won’t do as well. There are welders leaving some schools making 100K their first year but they’ll be putting in some overtime for sure. That’s not the standard by any means but it does show what is possible.”
Bottom line, don’t expect to get rich as an entry-level welder—but a wealth of opportunities await you. Welding skills are highly transferable, so a welder can move from one area or one employer to another in pursuit of a better salary or a more suitable place of employment.
Welding has provided a comfortable living for David Sinquefield, who owns MPD Welding in Grand Rapids. Much of MPD’s work is welding molds for plastic automotive parts. He owns his own home and usually once a year, he takes a month off to visit the Caribbean—although this year he couldn’t fly there because of Covid restrictions. (Also, GM was keeping them busy welding respirators!)
“I’ve never collected an unemployment check in my life,” he said. “Our welders are making over $38 an hour, out top guys—with complete, full benefits.”
What training is required to become a welder?
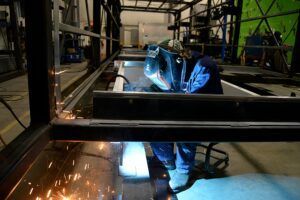
Unlike trades such as electrician, welders are not required to gain a certification to practice their craft for the most part. Nor are they required to go through a four- to five-year apprenticeship. All that’s required to be a welder is the skill—which requires a lot of practice and some sort of training. Most aspiring welders attend technical school or community college programs. Welding training ranges between seven months and two years of hands-on instruction.
Some welders start out as laborers, and the on-the-job training they earn allows them to advance in the field without ever attending a welding training program at a vocational or trade school. That said, employers usually want someone with training, because even welders with formal training still often have to receive several additional months of on-the-job training, depending on their employer. Some employers will require a certification.
Brown Dog Welding in Detroit offers welding workshops for beginner to experienced welders. The 3- to 4-hour workshops allow people to actually weld an item they can take home.
Brown Dog provides all welding materials and equipment and personal protective equipment. Attendees will leave the worship with an item they actually welded and a Miller Welding Gas Tungsten Arc Guide
David’s been welding since he was in the Army in 1969. “I was a mechanic, but where I worked was right next to the welding shop, so I gave it a try. I knew it was what I wanted to do with my life. After the service, I drove truck for a welding shop owned by a friend of my father-in-law. Within about a year, I was running one of the shifts—with no formal training.”
It’s worth noting that many prospective welders come to the craft having welded as a kid, in high school shop class or on dad’s farm, so they enter their professional education with a running start.
For this part, Jason took welding classes in high school but his education began in earnest when he joined the Marine Corps. The Marines put him through a 6-month, 40-hour-a-week training program.
Is welding dangerous?
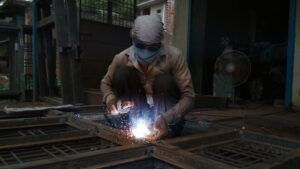
There are plenty of hazards to be aware of when it comes to welding. The risk of electrocution, fire and explosion, burns, electric shock, vision damage, to name a few. Dangers abound. For example, the plume of smoke that rises from the spot of welding or cutting is a mixture of diverse metal fumes and gases. Prolonged exposure has been associated with different types of cancers and other serious health effects.
But if you’re trained properly and you’re using all the correct gear, welding is no more dangerous than any other profession, said Jason.
What separates great welders from good welders
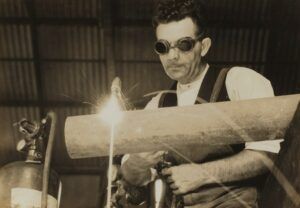
“Simple,” Jason says. “Passion.” If the topic of conversation never veered from welding, he’d be quite happy. “I love everything about it!”
“For some people, it’s just a job,” he said. “But for the Arc Junkies, they can’t get enough of it. You can always diver deeper, explore more, learn more. The more I learn about welding, the more I realize I don’t know anything about welding.”
David agrees about passion, adding, “A guy who doesn’t give a crap, he’s not going to put out great work—and he’s not going to last long in a welding shop.”
Did you like this post? You may also like:
Everything you need to know about becoming a plumber
Everything you need to know about becoming an electrician
Everything you need to know about becoming a carpenter
Everything you need to know about becoming a roofer
Everything you need to know about becoming an HVAC tech
Everything you need to know about becoming a mason
Everything you need to know about becoming a painter
Was this blog post helpful for you? Why not subscribe to our blog? It’s free. Just input your email address below. We promise we won’t spam you. However, as our way of saying thanks for subscribing, we’ll send you our e-book, “4 Things to Consider When You’re Looking for a Temporary Staffing Firm.”
Subscribe
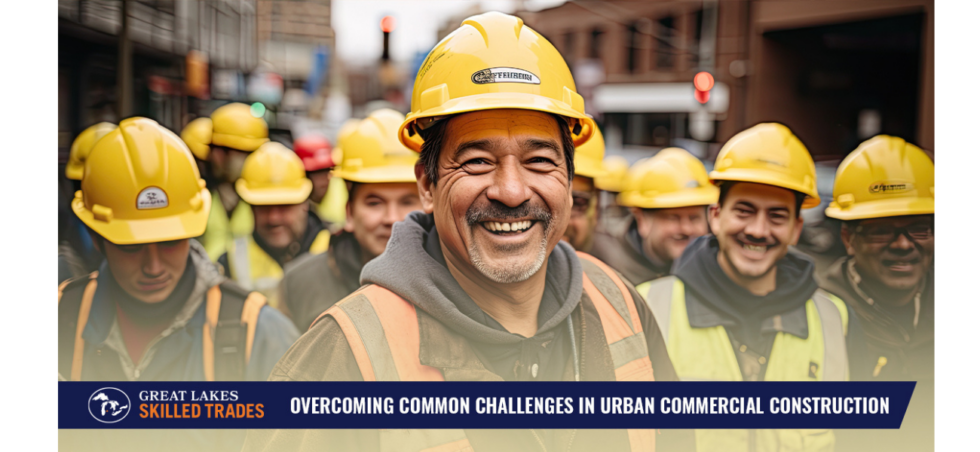