Contractor, how tech-savvy are you?
Do you use any apps on your smartphone? How about a drone—have you ever used a drone to survey a construction site?
Probably not. The construction industry has been a relatively conservative one, slow to adopt innovative materials, technologies, and processes.
But construction technology can boost productivity, enable collaboration, give greater control of the value chain, and shift a contractor toward data-driven decision-making.
“There’s so much pressure and risk associated with projects that people tend to behave with hyper cautiousness,” said John Palmer, Associate Director for Technology with the Construction Industry Association. “They usually aren’t willing to try something new and adjust if needed—trial and error.”
Here is a look at eight technologies that are changing the landscape of the construction industry.
Construction management software
Construction management software is a project management platform that helps companies with processes such as budget management, communication, decision-making, and job scheduling. Its goal is to make construction business processes a lot easier through automation.
An example is monday.com, which is used for numerous industries, not just construction. They call their product a “Work OS,” but you might also have heard of the term “workforce management platform.”
“When you think of construction, you think of all the regulations and approvals and signatures—getting the back office to talk to the front. Imagine even a small improvement in your operational efficiency,” said Matthew Burns, Startup Ecosystem Leader with monday.com. “If you think of time spent as a direct dollar cost, imagine how much saving five-plus hours a week per employee would mean to your business. That’s only the beginning with a Work OS.”
Robots and Drones
Robots are used to perform difficult, repetitive tasks. For example, Construction Robotics’ semi-automated mason can install 200 to 250 bricks per hour, compared to a human’s capability of 250 bricks a day!
The most common robots used on construction sites are drones. They make surveying quick and simple. Drones can spot potential hazards and track progress. Some contractors even use drones to deliver materials to the construction site. Who needs trucks?
Drones can monitor sites for safety hazards and give the foreman a quick view of the site without being physically present.
AI and Machine Learning
Artificial Intelligence is when a machine mimics human cognitive functions such as problem-solving and pattern recognition. Machine learning, a subset of AI, uses statistical techniques to give computer systems the ability to “learn” from data, without being explicitly programmed.
For example, requests for information, open issues, and change orders are standard in the industry. Machine learning is like a smart assistant that can scrutinize this mountain of data. It then alerts project managers about the critical things that need their attention.
Contractors are using AI and Machine Learning for “predictive design”—that is, taking multiple factors into account such as weather or location. Machine learning can be used to explore different variations of a solution and create design alternatives. Using historical data, AI can predict cost overruns. AI can monitor a worksite for safety hazards, using recognition technology to tell if a worker is wearing the correct PPE.
Building Information Modeling
BIM started as a way of creating 3-D models so interested parties could look at all the dimensions of space and avoid problems. But it has elevated—become more intelligent. For example, it can consider the cost of materials and scheduling.
BIM allows contractors, engineers, and architects to collaborate on coordinated 3D models, giving everyone better insight into how their work fits into the overall project. They can use the model to improve design before it’s built and solve problems along the way.
Apps
You can use them wherever you are—the trailer, your truck or even your home kitchen table.
ANC Construction in Chicago uses the Hubstaff time card app. It lets President Javier Enciso Jr. know where his crews are, what they’re doing and when they’re clocked in—all from his smartphone.
For example, with Hubstaff, Javier can set up a digital barrier known as a “geofence.” Once a crew member enters or leaves a set area, their smartphone’s GPS will automatically clock them in or out.
“I wanted workers to clock in daily on each job site, but I no longer had the time to do it manually,” he said. “Knowing how long workers are taking to move from one job to another or exactly where your workers are at all times is vital in construction.”
Virtual or augmented reality
What’s the difference, you ask? Virtual reality is being totally immersed in a digital world through a special mask of some kind. Augmented reality just adds digital elements to your “real” view.
Either way, the technologies can help you and your customer gain a better understanding of the project right from the very beginning—even large, complex projects. With a simulation of proposed changes, you can quickly know if it’s the right solution or needs tweaking.
What if you used AR/VR to create a building model with BIM technology and then to take a sightseeing tour and literally walk through and around it?
3-D printing
Sometimes referred to as Additive Manufacturing, 3-D printing is the computer-controlled sequential layering of materials to create three-dimensional shapes, often prototypes, for example. 3-D printing allows contactors to create project models that show how the project would look finished.
3-D printing provides the capability to either prefabricate offsite or directly on-site. Compared to traditional building methods, now it is possible to print materials important for prefabrication and have them ready to use immediately.
Materials such as metal can be costly to print, and in this case, it may be more cost-effective to print a mold and then to use that to create the item.
Applicant tracking system
Larger contractors with HR departments and recruiters make great use of Applicant Tracking Systems, a software for recruiters and employers to track candidates throughout the recruiting and hiring process.
Most skilled trades staffing firms also use ATS.
“Everyone knows about the skilled trades talent shortage. There are a ton of job openings out there. You need to make your firm stand out,” said Dustin Ide, General Manager of Great Lakes Skilled Trades in Grand Rapids. “We’re treating the available workers like customers. We sent out text message blasts. We hit them where they live—their smartphones. The point is to build a relationship by ‘touching’ them multiple times. They may not be looking now, but you have to stay top-of-mind with them, so they’ll think of you when they are looking.”
“Technology can bring huge productivity gains for contractors,” John Palmer of the Construction Industry Association said. “But to get there, owners, contractors, and suppliers need to adopt a more balanced view of risk and opportunity. The balance is way out of whack. So often now, it’s assumed the risk exceeds the opportunity to improve and the ‘safe’ route is the one taken.”
Did you like this post? Check out How contractors can team up with local schools
Was this blog post helpful for you? Why not subscribe to our blog? We’ll post on ways contractors can grow their business. It’s free. Just input your email address below. We promise we won’t spam you.
Subscribe
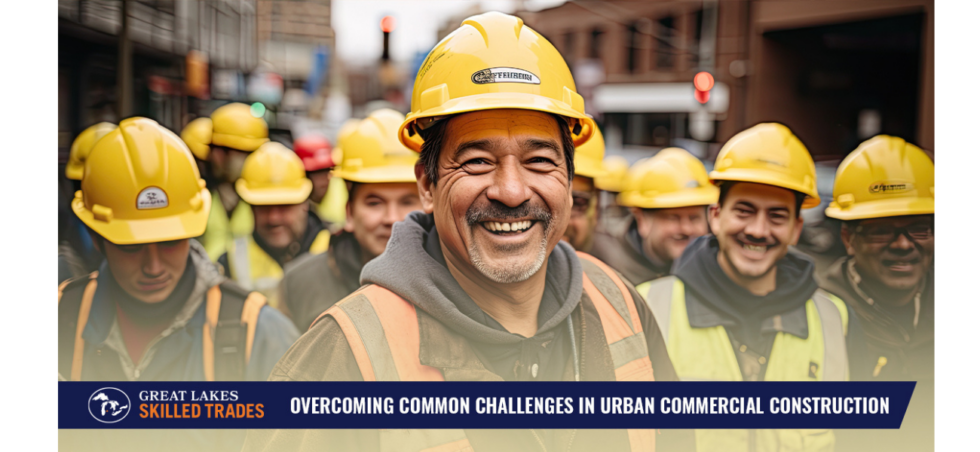